The headlines are making for tough reading but resilience and innovation is needed in the metals industry.
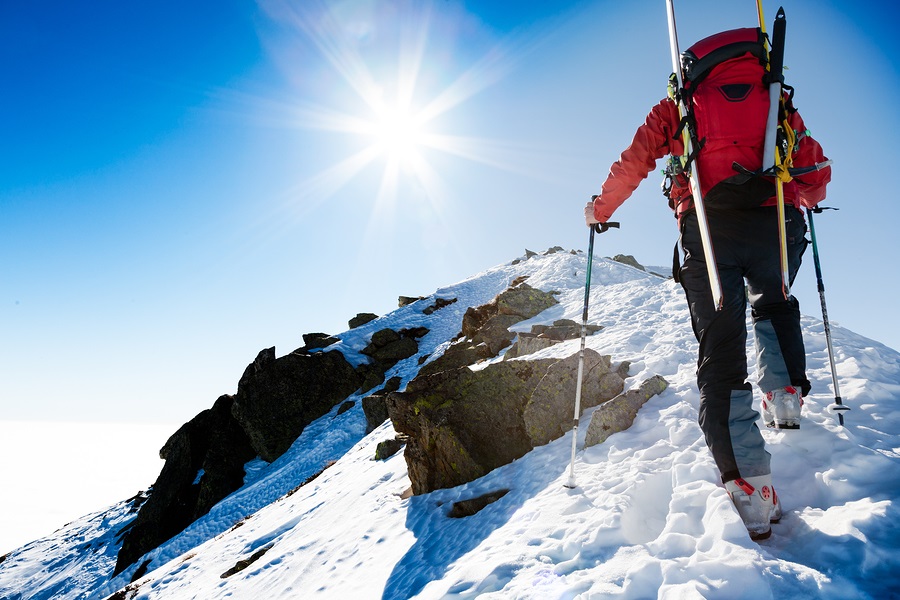
A quick Google search on the state of the metals recycling landscape is unlikely to pull up particularly positive results at the moment. At the start of 2016 we learned that scrap prices were at virtually an all-time low, and only recently we read comments that the global secondary metals market is the toughest it’s been for 30 years.
Findings from an online UNTHA UK poll in late 201 suggested similar feelings of frustration and uncertainty. When asked ‘Do you think it’s still possible to make money in the metals industry, in the current depressed market?’ 44% of respondents encouragingly said yes, but the majority didn’t believe it feasible. 12% also didn’t have an answer, which perhaps speaks volumes.
Those in this field could be forgiven for feeling a little downhearted as they plan for the 12 months ahead. However, this is an industry full of ‘mettle’.
Recent figures suggest that UK metals recycling is a £5.6bn industry that employs 8,000 people. That’s something to be proud of. As is the fact that smelting old scrap to produce new metal is one of the oldest ‘circular’ concepts there is. The challenge isn’t that we don’t know how to process, recycle and trade metals successfully. It’s that there are so many external forces at play, restricting how we do it!
Many such forces are admittedly beyond our control. But, any business plan must take into account political, economic, social and technological factors, and, whilst these factors may admittedly be quite sizable at present, we can – and should – look to overcome at least some.
In this respect much depends on innovation and a receptiveness to change. So, looking particularly at technology, the factor I can speak most confidently about, where do the opportunities lie?
Of course there are some organisations that ‘like what they know’. This explains why they continue to use traditional shear equipment to cut metals down, because the perceived high-wear nature of the application would make alternative methodologies too expensive. But failure to look beyond big, cumbersome pieces of kit means ever-smarter sorting, grading, separation and size-reduction technologies are being overlooked.
It is these technologies that will boost the efficiency, sophistication and potential revenue yield of metal recycling lines. How? By focusing on metal recyclate quality.
Too many valuable metals remain ‘locked’ in complex products such as uPVC windows and end-of-life vehicles. They need to be liberated with more advanced kit and their value realised. Elsewhere, in MRFs and alternative fuel production plants, Fe and non-Fe magnets extract metals from the lines for maximum waste hierarchy compliance. But up to 50% of the material can be contaminated with substances like plastic film, which renders the metal worthless. In fact, in recent times, operators haven’t just struggled to generate revenue from the material – they’ve had to pay a disposal fee!
However, these contaminated metals can be cleaned using technology such as a high torque, low-wear four-shaft shredder, plus density separators and other sorting technologies such as NIR for further segregation. And the result? Maximum volumes of high quality ferrous and non-ferrous scrap for resale.
Of course investment is needed in such a new process, and it is understandable for recyclers to try avoid further expenditure. But whilst the temptation is to sit and wait for change, this often perpetuates the problem. Instead, the focus should be on a payback period as fast as 18 months, and the future, because it can be bright!
--------------
The Author
Marcus Brew is Managing Director of UNTHA UK.