From BMRA service member Lindemann Metal Recycling
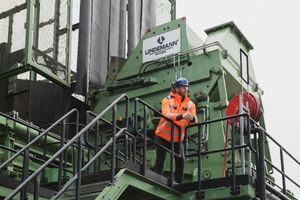
Metal recycling still involves a lot of physical metal bashing. But two new advances are significantly improving the efficiency and sustainability of the process. Here we look at Shredder Drive Assistant and Variable Frequency Drive.
Giant, heavy, fast-spinning rotors crashing into scrap steel to shred it generates a lot of energy – and consumes a lot too. So, any innovation that can improve the process such that it achieves a higher throughput or lowers the energy requirement is to be welcomed. And not just for its boost to profitability – cutting electricity consumption can have a significant impact on lowering the carbon footprint of metal recycling operations.
As it has done for more than a century, BMRA service member, Lindemann Metal Recycling, remains at the forefront of innovation in the sector. Two of its latest technologies have the potential to deliver significant improvements in process throughput and energy reduction.
Shredder Drive Assistant (SDA)
Boosting operational efficiency – that’s the goal of Shredder Drive Assistant (SDA). An upgrade that is compatible with almost every Lindemann shredder in the field today, the Lindemann SDA is now routinely producing double-digit percentage savings, enabling the upfront cost to be rapidly retrieved.
Attached to the shredder’s controller in just a few hours, with negligible modifications required, this smart feed-roller device comprises a separate control box and a new sensor for the feeding system. Monitored from within the operator’s cabin, it acts rather like an aeroplane’s autopilot, overseeing all relevant process variables to optimise feeding for constant, maximised throughput.
“Even if you have a very good operator, recent real life installations of SDA have seen the system reduce operational expenses by a further 7-10% per tonne,” states Daniel Deegener, Senior Product Manager Shredder Systems, at Lindemann. “Unlike many machines that suffer from operator abuse, shredders are often treated too sympathetically, especially when operators are getting tired. So, SDA brings the shredder up to its operational limits, maximising its efficiency – but always while monitoring component temperatures and Ampere hours, ensuring it does so safely and with the maximum economy.”
With the operator poised to manually intervene should the material flow begin to clog, or to remove dangerous items, such as gas bottles, the SDA is able to control operation in the most energy-efficient way. “Electricity suppliers usually bill operators according to the highest peak per quarter, which typically happens when you suddenly throw in a car – even if that’s the only one you shred all year,” Deegener continues. “By shaving those peaks customers can make huge savings.”
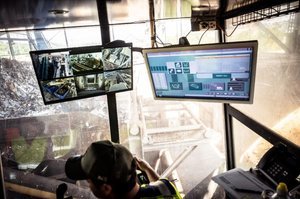
Variable Frequency Drive (VFD)
Another pioneering shredder technology with significant potential for saving energy is Variable Frequency Drive (VFD). By their nature the rotor in a shredder must cope with constantly changing performance demands, due to the intermittent nature of material feeding into the machine. When the shredder rotor is loaded with scrap metal to process, the rotor speed briefly decreases. The motor then tries to quickly accelerate the large and heavy rotor back to its normal speed. This constant change between slowing down and speeding up of the shredder rotor places high demands on the motor. Therefore, the efficiency of shredder operation is largely determined by the motor load’s quality monitoring and speed control. The aim is to return to the normal motor speed as quickly as possible – and this is where VFD excels, resulting in potentially considerable energy savings.
SDA and VFD are two innovative examples of new technologies making a significant impact on the established process of recycling scrap metal, which together improve throughput and lower both costs and environmental impact.